Best practices for operating the Hougen HMD905 Magnetic Drill safely are essential for ensuring efficient and secure drilling at home. By following these safety guidelines, DIY enthusiasts can enjoy their home improvement projects while minimizing risks and maximizing the performance of their magnetic drill.
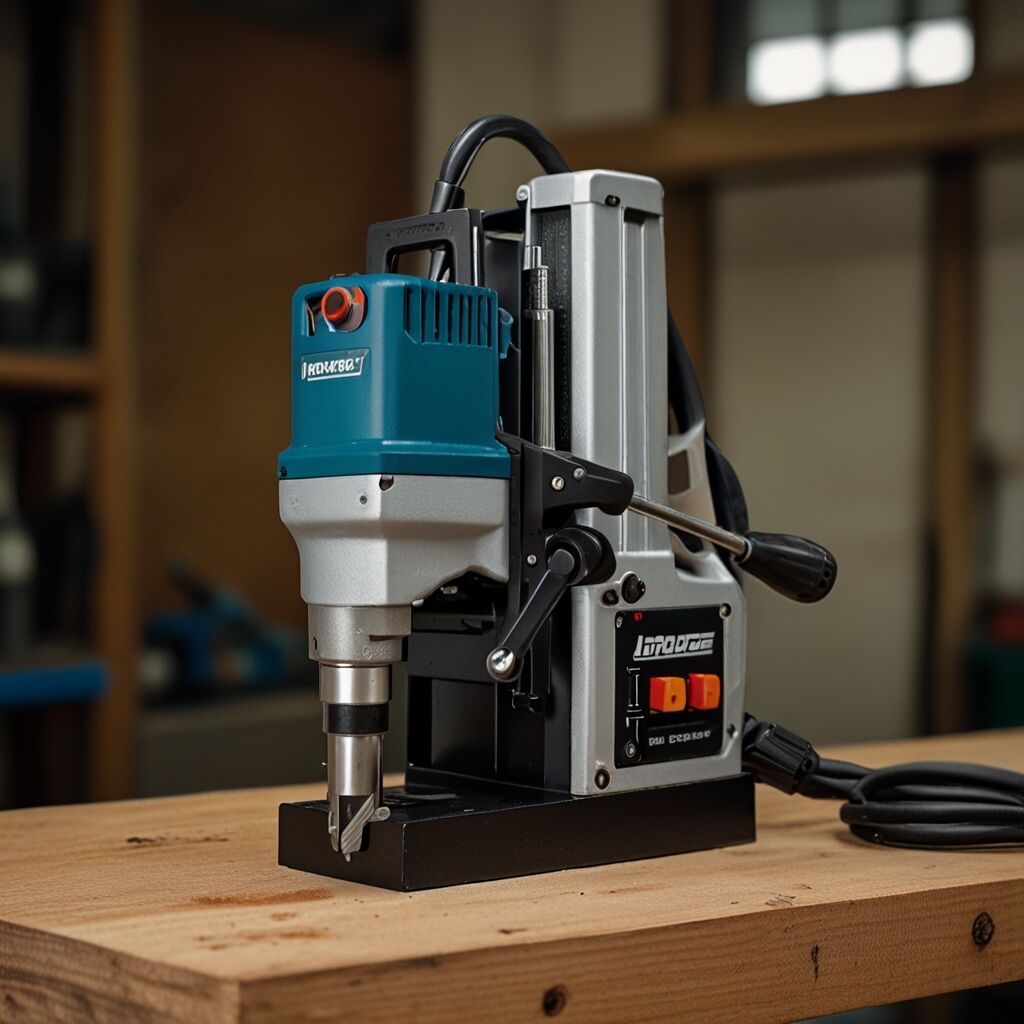
Understanding Key Safety Procedures for the Hougen HMD905 Magnetic Drill
The essential safety guidelines for using a magnetic drill like the hougen HMD905 include checking for proper setup, ensuring a stable surface, and using the drill as instructed. To prevent accidents while operating the Hougen HMD905, ensure a secured workpiece and maintain a clear workspace while working with the drilling tools.
Necessary personal protective equipment (PPE) for magnetic drilling includes safety glasses, gloves, and hearing protection. In case of an emergency with the magnetic drill, immediately disconnect the power and follow the manufacturer’s emergency procedures to stop drilling efficiently, ensuring safety at all times.
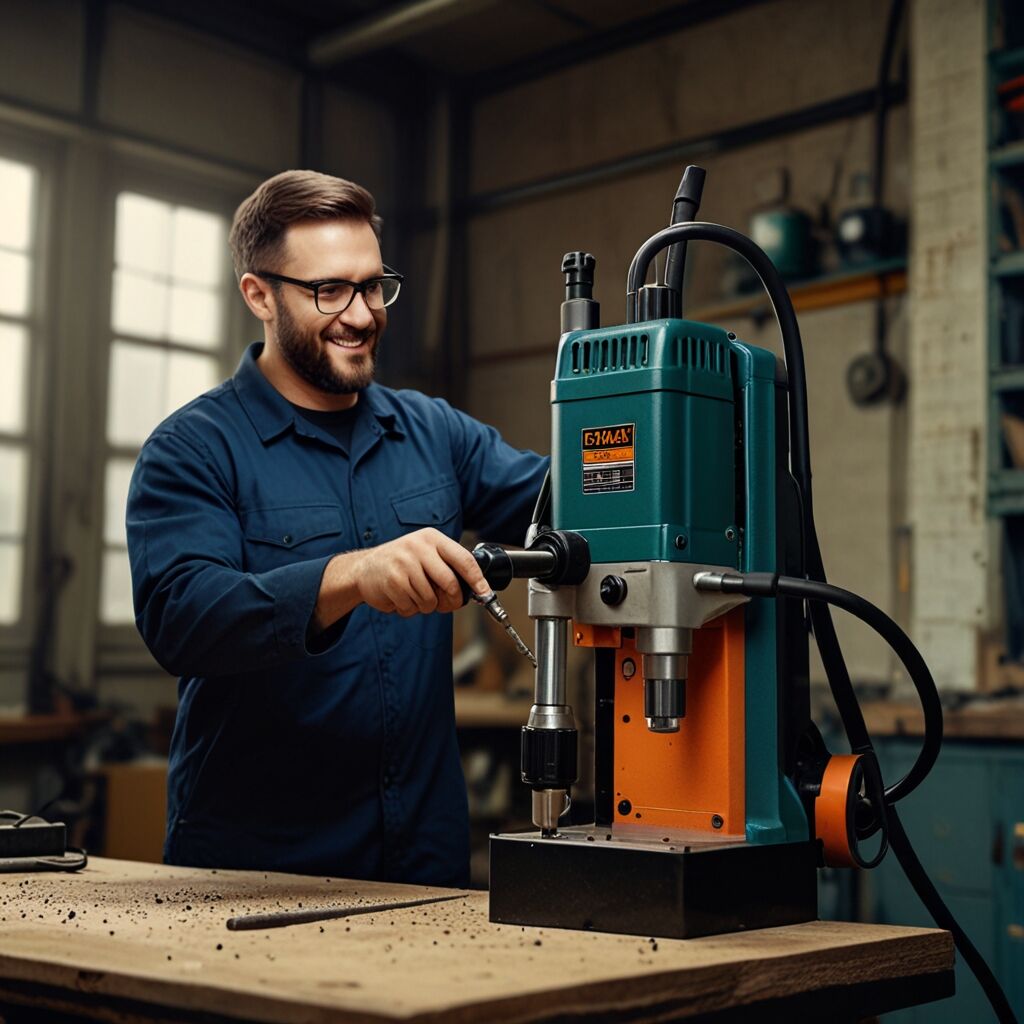
What are the top recommendations for ensuring safety while drilling?
Perform at least two safety checks before starting the Hougen HMD905 to verify that everything is in proper working order. For safe operation of the drill, maintain a minimum distance of at least three feet between others and the drilling area to minimize risks associated with flying debris.
Ensure that at least one emergency stop is easily accessible during operations to quickly disconnect the power in case of an unforeseen issue. Wearing three items of PPE, such as goggles, gloves, and a hard hat, provides the best protection while operating the magnetic drill.
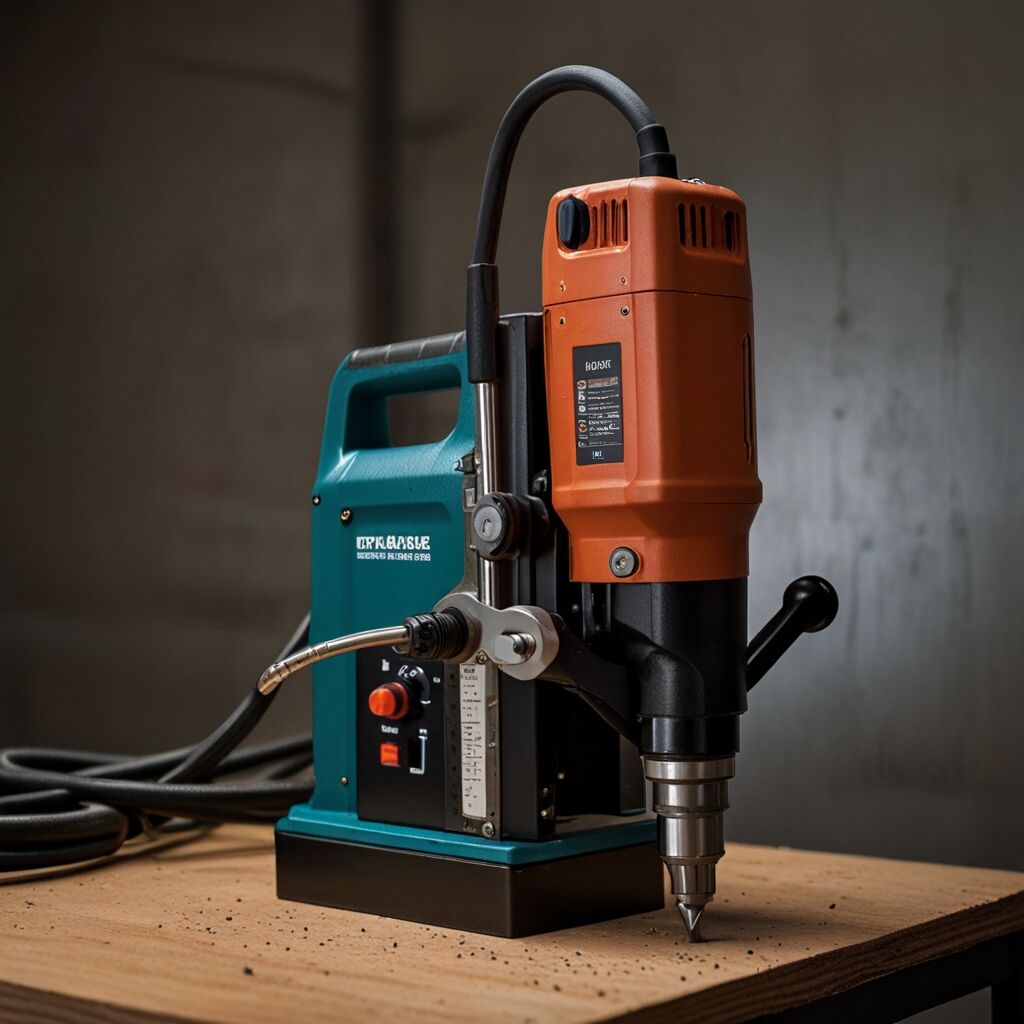
Best Practices for The Safe Handling of the Hougen HMD905 Magnetic Drill
Best handling practices for a magnetic drill include correctly securing the drill to the workpiece using its powerful magnet. To maximize the stability of the Hougen HMD905 during use, ensure the surface is clean and level, reducing any potential wobble or unwanted movement.
Regular maintenance tips to prolong the life of the magnetic drill consist of checking the cable for frays, inspecting the magnet, and lubricating moving parts. When transporting the magnetic drill, always use a sturdy case to protect it from damage, and keep it upright to avoid any mishaps during movement.
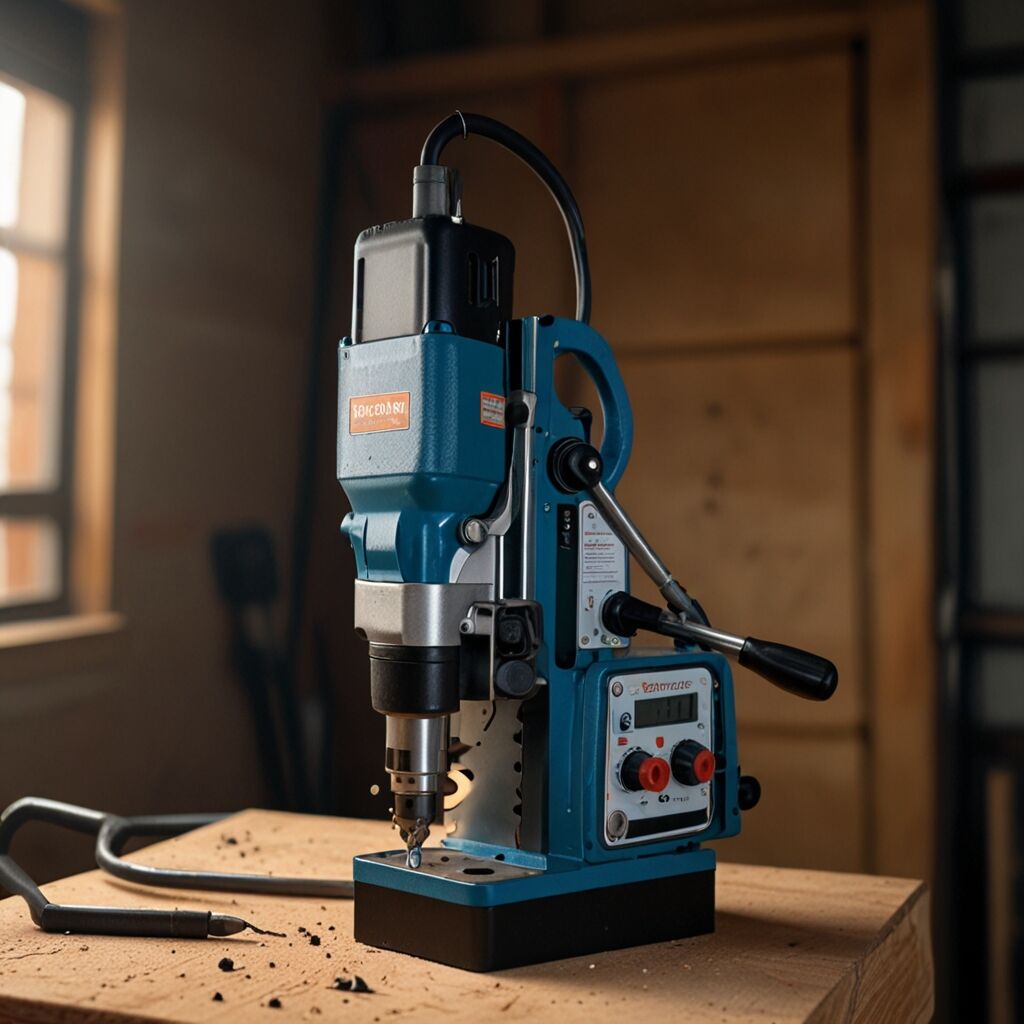
What guidelines should be followed while operating a magnetic drill?
There are ten essential safety guidelines for operating magnetic drills, which cover proper handling and operational procedures. The recommended maximum weight capacity for safe operation of the Hougen HMD905 is around 5,000 pounds to prevent any strain on the drill and user.
Users can operate the drill for up to two hours continuously before taking a break to rest and cool down the equipment. Cleaning and maintaining the drill parts should be done after every use to ensure the best performance and reliability of the magnetic drill.
Safety Checks and Precautions for the Hougen HMD905 Magnetic Drill
Essential safety checks before using the magnetic drill include inspecting the power cord, verifying the magnet’s strength, and ensuring the drill’s bits are sharp. Regular inspections enhance safety while drilling, as it helps to prevent breakdowns and ensures the equipment is constantly in the best working order.
To avoid electrical hazards, keep the drilling environment dry and check for water exposure around electrical connections. Securing the work surface before starting the drill ensures stability, reducing the risk of accidents during operation with the Hougen HMD905 Magnetic Drill.
What inspection protocols should be in place for magnetic drills?
Weekly inspections on the drill should be performed to ensure all parts function properly and meet safety standards. The maximum allowable wear on drill bits before replacement is typically around 1/16 of an inch to ensure reliable cutting performance and maintain efficiency during use.
Test at least two safety switches before each use to guarantee that they function correctly, enhancing safety. For electrical connections, it is crucial to perform at least three checks to ensure all wires are secure and pose no risk of electrical failure during operations.