Efficient pipe installation is essential for both DIY enthusiasts and professionals seeking high-quality results. The Hougen HMD920 Drill offers a range of features that ensure reliable and effective drilling, making it an indispensable tool in home improvement projects and heavy-duty tasks alike.
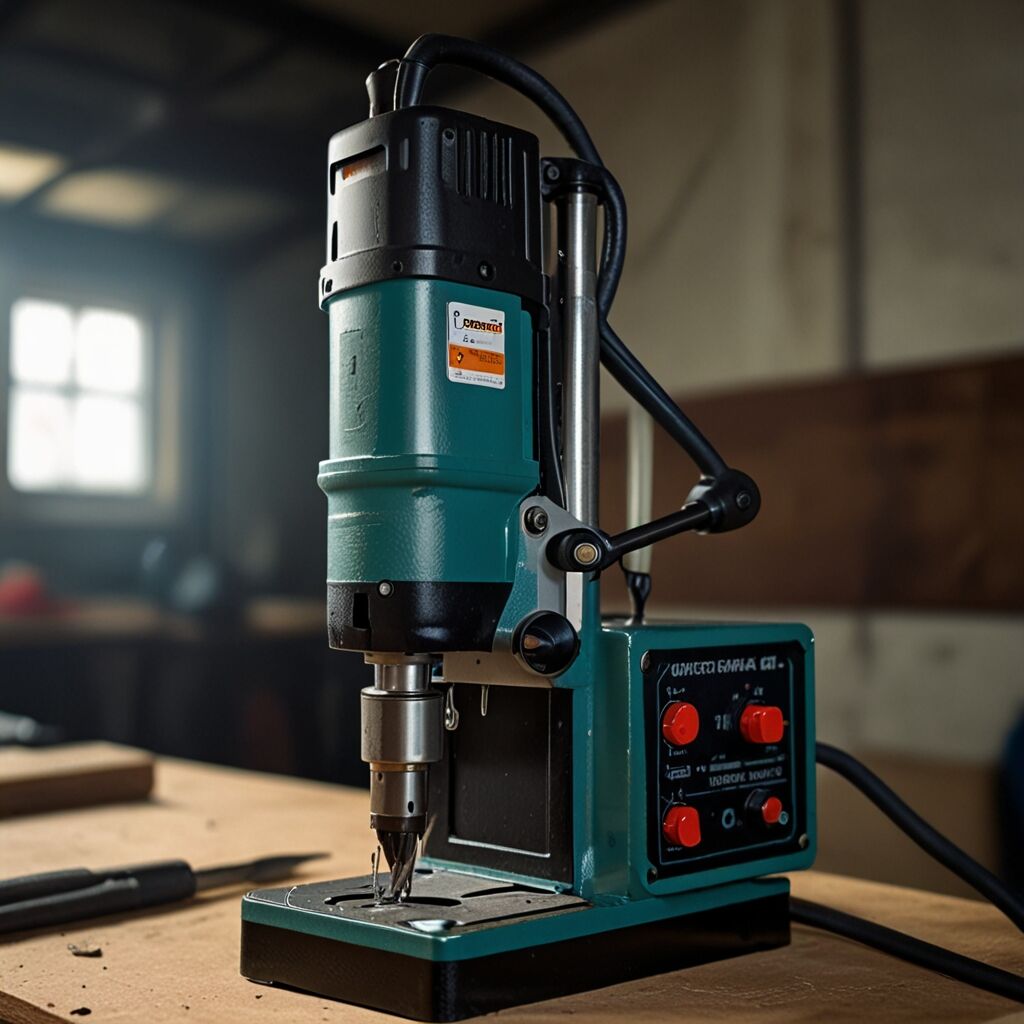
Efficient Pipe Installation Techniques Using the Hougen HMD920 Drill
Best practices for using the Hougen HMD920 Magnetic Drill for pipe installation include securing the workpiece firmly and using the correct drill bit for the material type, ensuring precision and quality. Essential safety measures involve wearing safety goggles and heavy gloves to protect against metal shavings and ensuring the drill’s stability to avoid accidents. A typical installation can take anywhere from 30 minutes to two hours, depending on pipe material and diameter, with experienced operators achieving quicker setups. Common mistakes to avoid include not using cutting fluid, which leads to overheating, and forgetting to check the drills alignment, resulting in uneven holes.
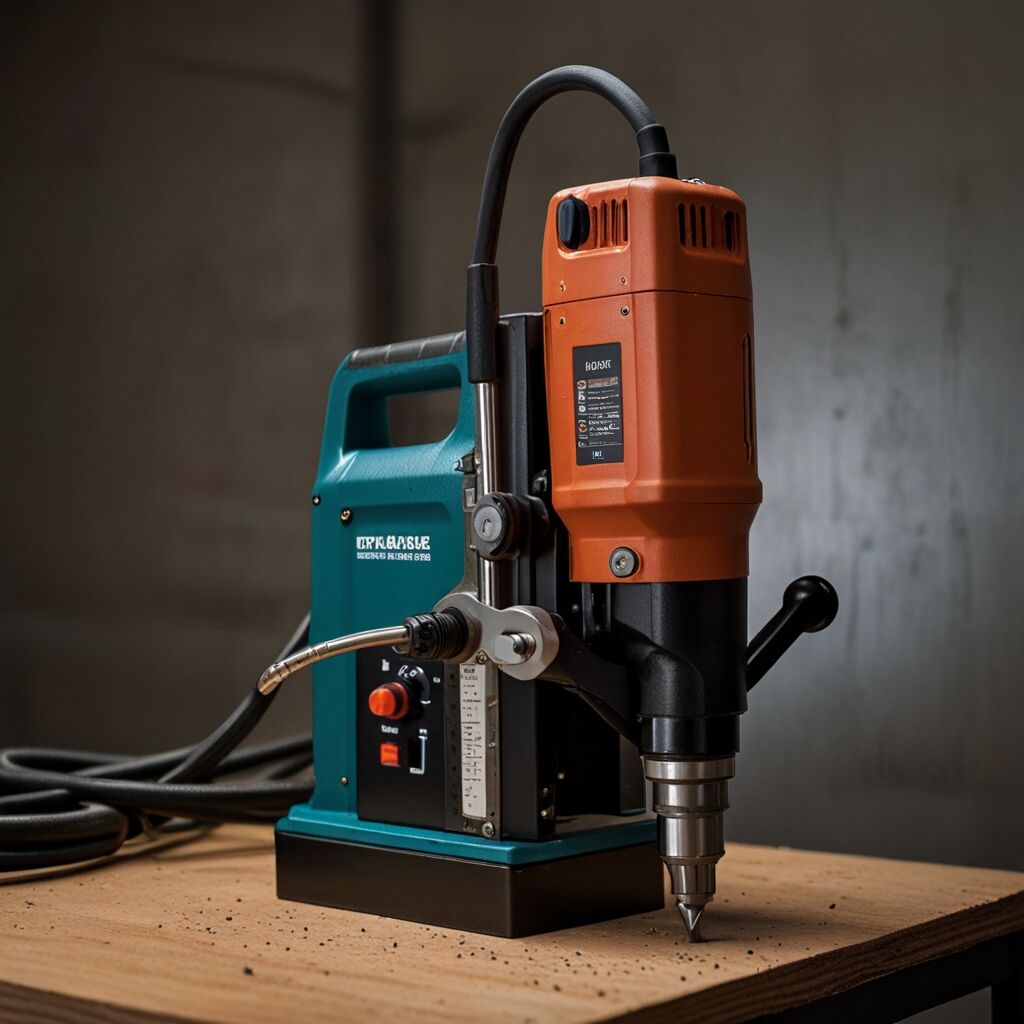
How can proper setup improve drilling performance and accuracy?
Proper setup significantly enhances drilling performance and accuracy by creating optimal conditions for the Hougen HMD920 115-Volt Magnetic Drill. The ideal distance between the drill and pipe should be as close as possible, typically around one inch, which maximizes the drill’s magnetism and stability during operation. For different materials, using at least three drill bitshigh-speed steel (HSS), cobalt, and carbide-tippedis recommended to achieve the best results. The ideal speed setting varies; for steel, a setting between 100-150 RPM works best, enabling operators to drill up to five feet per hour with the right techniques.
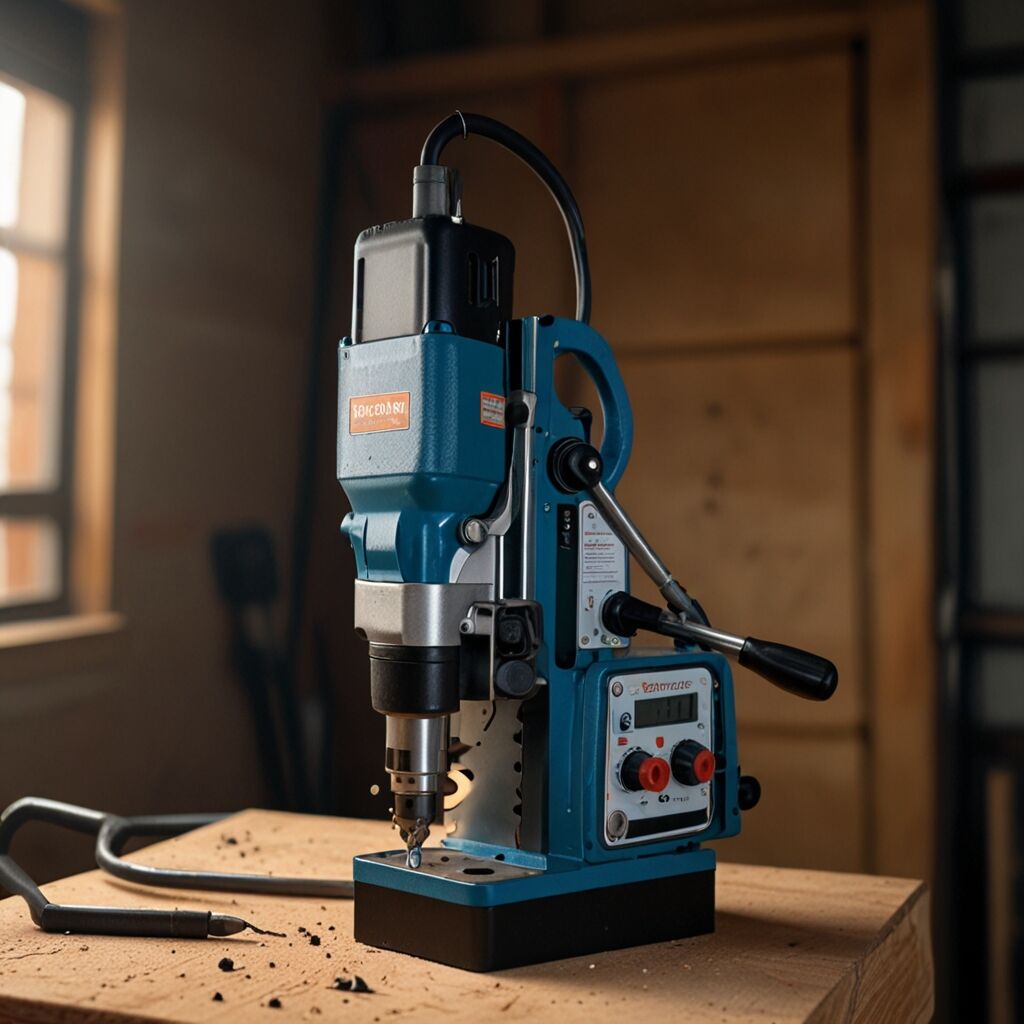
Maximizing Efficiency in Pipe Installation with the Hougen HMD920 Drill
Features of the Hougen HMD920 enhance drilling efficiency by incorporating a powerful magnet, adjustable speed settings, and quick-change bit systems, allowing for seamless transitions between tasks. The drills portability benefits pipe installation projects by enabling users to move easily across different job sites without sacrificing power or functionality. Energy consumption levels are impressively low, as the HMD920 Magnetic Drill is designed to operate efficiently, often using less power than traditional drills. Regular maintenance practices, such as cleaning and lubricating the motor, significantly affect drilling efficiency by prolonging the tools lifespan and ensuring peak performance.
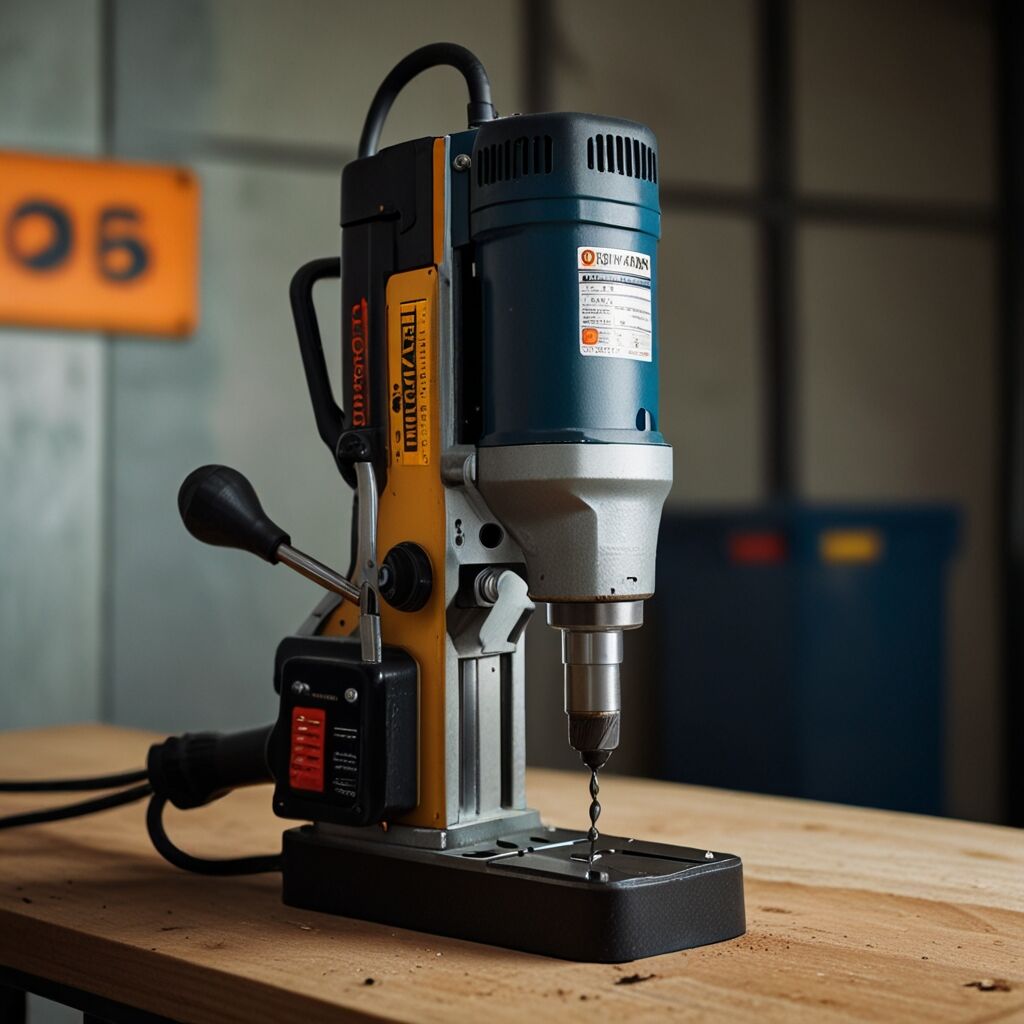
What advancements in technology boost drilling efficiency for pipes?
The Hougen HMD920 Magnetic Drill includes several advanced features such as automatic shutoff, onboard chip collection, and an improved cooling system that boosts drilling efficiency. Skilled operators can expect around 10-20 downtime due to waiting for materials or tool changes, leading to effective project timelines. Latest materials used in the drill are roughly 30 stronger than standard options, designed for enhanced durability and reliability under high-stress conditions. With optimal setup, users can complete up to 10 installations in a day, maximizing productivity with the right tools and techniques.
Cost-Effective Pipe Installation Solutions with the Hougen HMD920 Drill
The average cost of using the hougen hmd920 115-volt magnetic drill for pipe work can range from $150 to $500, depending on the complexity of the installation. When compared to traditional methods, utilizing the HMD920 can reduce costs by up to 25, thanks to decreased labor and material waste. Financial savings become apparent as efficient drilling reduces both material and time expenses, making projects more budget-friendly. Maintenance plays a crucial role in lowering long-term costs, as a well-maintained drill operates reliably for years without the need for costly replacements.
What factors contribute to reduced costs during pipe drilling projects?
Using the Hougen HMD920 Magnetic Drill can save an average of 30 in labor hours by significantly speeding up the drilling process. The cost per drilled hole, when using this innovative system, often drops to under $10, making it more economical than conventional drilling methods that can exceed $20 per hole. Regular replacements of drill bits are typically minimal, with only 2-3 parts needing replacement annually for effective operation due to high-quality materials. By optimizing tools and processes, project budgets can save upwards of 15, leading to more efficient project completion and happy DIYers.